Hydraulic Tube Fittings Manufacturer: Elevating Industry Standards
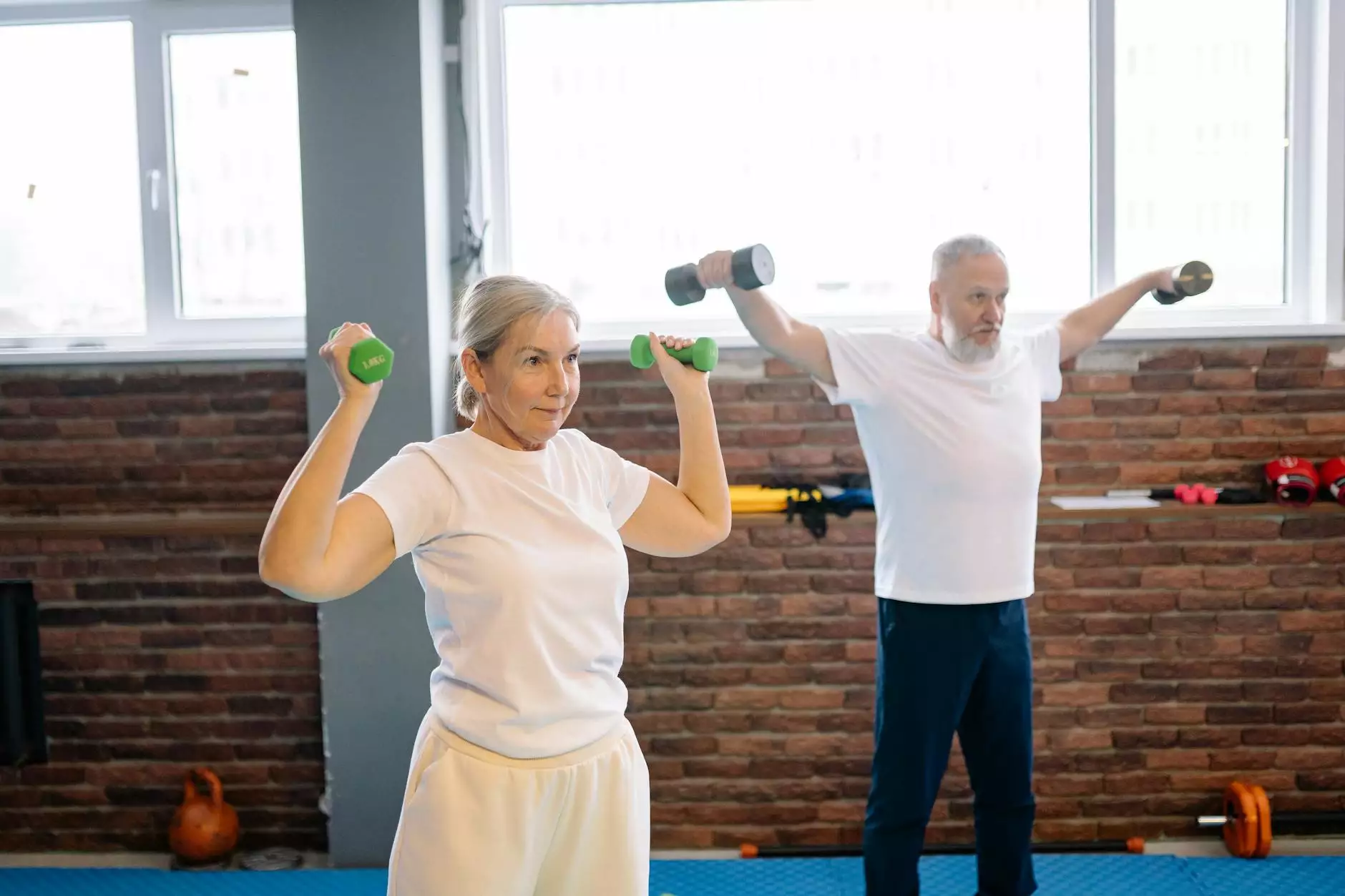
Hydraulic systems are crucial in various industries, powering machinery and supporting operations that demand robust and reliable equipment. Among the essential components of these systems are hydraulic tube fittings, which play a pivotal role in maintaining fluid flow and pressure in hydraulic circuits. This article delves into the significance and intricacies of hydraulic tube fittings, focusing on a premier Hydraulic Tube Fittings Manufacturer, to help you understand the value of investing in high-quality fittings for your operational success.
Understanding Hydraulic Tube Fittings
Hydraulic tube fittings are engineered components that connect tubes and pipes in hydraulic systems. Their primary function is to create a tight seal and prevent leakages, ensuring efficiency and safety in operations. Let’s break down some essential features and types of fittings used in hydraulic systems:
- Functionality: Hydraulic fittings must withstand high pressures and aggressive environments. They are designed to resist both physical and mechanical stresses.
- Types: There are several types of hydraulic fittings, including:
- Compression Fittings: These fittings compress the tube against a tapered surface, providing a secure seal.
- Flared Fittings: Designed to create a strong connection through a flared end of the tubing.
- Pipe Threaded Fittings: These fittings use threaded connections, offering versatility in installation.
- Materials: They are commonly made from materials such as stainless steel, brass, and carbon steel, chosen for their strength and resistance to corrosion.
Why Choose an Established Hydraulic Tube Fittings Manufacturer?
Partnering with a reputable Hydraulic Tube Fittings Manufacturer like fitsch.cn ensures that you receive components with:
- Quality Assurance: High-end manufacturers implement strict quality control measures. They guarantee that each fitting meets industry standards and specific requirements.
- Cost-effectiveness: Reliable manufacturers offer competitive pricing without compromising quality, ensuring you get the best value for your investment.
- Expert Support: An established manufacturer often provides technical support and guidance, aiding you in selecting the right fittings for your applications.
Innovative Manufacturing Processes
The process of manufacturing hydraulic tube fittings has evolved significantly. Leading manufacturers now employ advanced technologies to ensure precision and quality. Here are some of the innovative methods commonly used:
- CNC Machining: Computer Numerical Control (CNC) machining allows for high precision in the manufacturing of fittings, significantly reducing human error.
- Hydroforming: This technique uses high-pressure fluid to shape fittings, ensuring uniform thickness and greater strength.
- Die Casting: An efficient process for producing complex shapes and maintaining tight tolerances, essential for high-volume production.
Customization in Hydraulic Tube Fittings
One of the standout features of a top-tier Hydraulic Tube Fittings Manufacturer is the ability to offer customized solutions. Here’s why customization in fittings is crucial:
- Tailored Solutions: Every hydraulic system is unique. Customized fittings can help you meet specific pressures, temperatures, and system configurations.
- Efficiency and Performance: Ensuring that the fittings are designed for your unique application enhances the overall system performance.
- Scalability: Whether you are an OEM or a large enterprise, having access to custom fittings allows you to scale operations without compromising on quality.
Durability and Reliability of Hydraulic Fittings
Investing in durable hydraulic fittings can lead to significant long-term savings. Here's why durability matters:
- Longevity: High-quality fittings withstand harsh environments, decreasing the frequency of replacements and repairs.
- Safety: Secure and reliable fittings minimize the risk of leaks, which can lead to safety hazards and costly clean-ups.
- Operational Efficiency: Reliable fittings ensure consistent fluid flow and pressure, vital for optimal equipment performance.
Best Practices for Selecting Hydraulic Tube Fittings
When it comes to selecting the right hydraulic fittings, consider these best practices:
- Understand Your System Requirements: Analyzing the specifications of your hydraulic system is essential. Consider pressure ratings, temperatures, and fluid compatibility.
- Consult with Experts: Engaging with manufacturers’ technical teams can provide insights into which fittings best suit your needs.
- Evaluate Material Choices: Decide on materials based on the operating environment and the type of fluids being used.
The Impact of Quality on Business Operations
Quality hydraulic tube fittings can make a significant impact on operational efficiency and the bottom line. Here's how:
- Reduced Downtime: High-quality fittings minimize the risk of breakdowns, leading to improved productivity.
- Cost Savings: Fewer replacements and repairs mean lower operating expenses over time.
- Enhanced Reputation: Companies known for using high-quality components often gain a competitive edge in the market.
Conclusion
Selecting the right Hydraulic Tube Fittings Manufacturer like fitsch.cn can significantly enhance the efficiency and reliability of your hydraulic systems. By prioritizing quality, customization, and innovative manufacturing practices, you can ensure that your business operations remain optimal and cost-effective. Investing in the best fittings not only addresses current needs but also positions your organization for future growth and success in an increasingly competitive landscape.
For businesses looking to maximize their potential, maintaining a strategic partnership with a trusted hydraulic fittings manufacturer is paramount. Explore the offerings at fitsch.cn to find solutions that align with your operational goals.
Hydraulic Tube Fittings Manufacturer