Enhancing Metal Fabrication: The Game-Changing Impact of Prototype 3D Printing
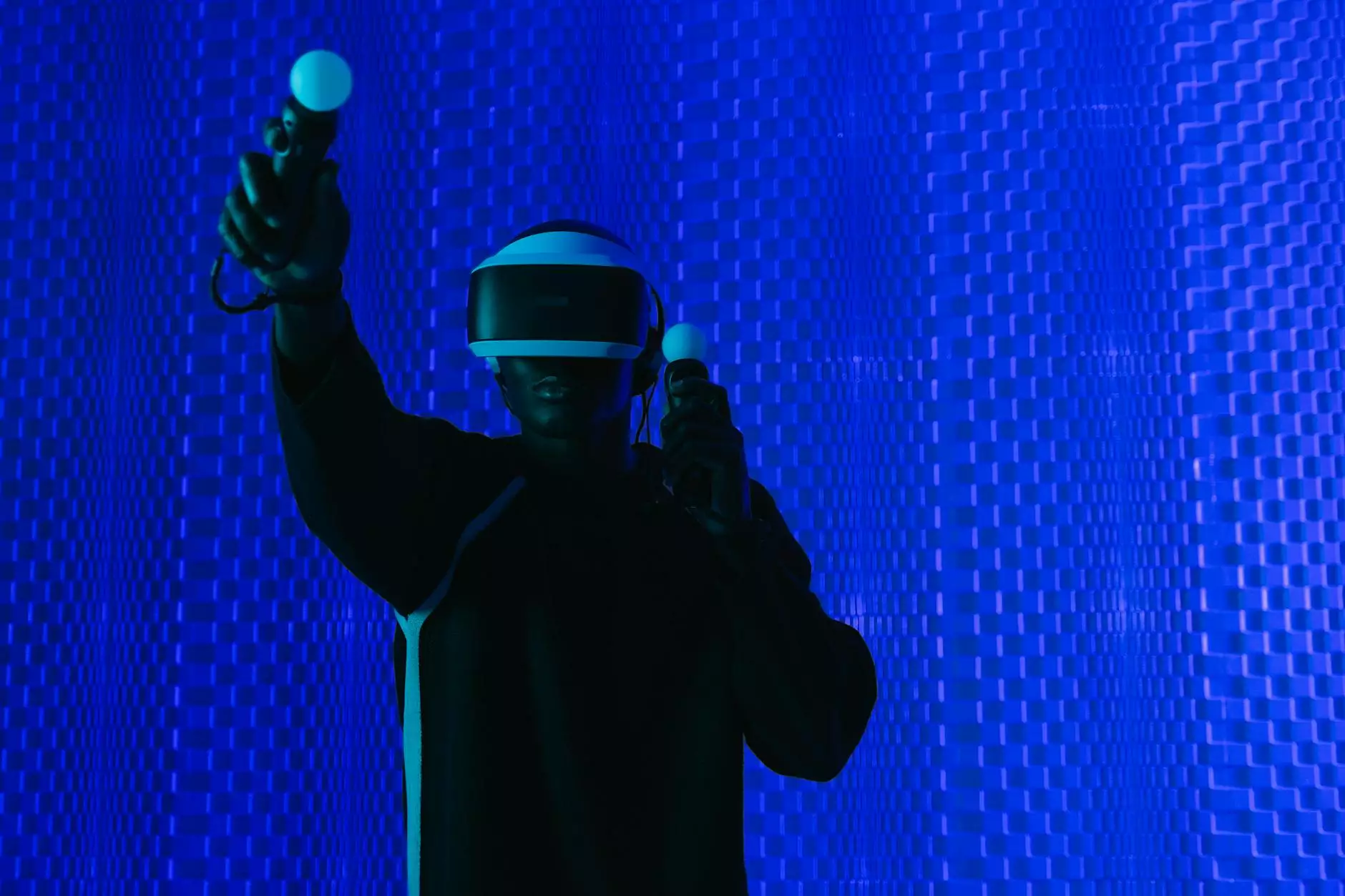
In the fast-paced business world, staying ahead means embracing innovation and technology. The rise of prototype 3D printing is transforming industries, particularly in metal fabrication. This article explores how 3D printing is changing the manufacturing landscape, focusing on its advantages for metal fabricators and its application in creating prototypes that accelerate product development.
What is Prototype 3D Printing?
Prototype 3D printing, also known as additive manufacturing, involves creating three-dimensional objects by layering materials based on digital models. Unlike traditional manufacturing, which typically involves subtractive methods (cutting away material), 3D printing builds objects layer by layer, allowing for greater design flexibility and resource efficiency.
The Basics of 3D Printing Technology
At its core, 3D printing technology utilizes computer-aided design (CAD) software to create a digital model of an object. This model is then sliced into thin horizontal layers, with a 3D printer depositing material to construct the item from the ground up. There are various methods of 3D printing, including:
- Fused Deposition Modeling (FDM): A popular method that uses thermoplastic filament.
- Stereolithography (SLA): Uses a laser to solidify liquid resin layer by layer.
- Selective Laser Sintering (SLS): Fuses powdered materials using lasers, suitable for metal and plastic parts.
The Importance of Prototyping in Metal Fabrication
Prototyping is a crucial step in product development. It allows manufacturers to test concepts, assess functionality, and make necessary adjustments before final production. Traditional prototyping methods, such as machining and molding, can be time-consuming and expensive. However, leveraging prototype 3D printing offers several benefits:
- Faster Production Times: 3D printing significantly shortens the lead time from concept to prototype.
- Cost Efficiency: Reduces material waste and cuts down labor costs.
- Design Flexibility: Allows for complex geometries that are difficult or impossible to achieve with traditional methods.
How Prototype 3D Printing Streamlines Product Development
By enabling rapid prototyping, prototype 3D printing simplifies the product development process, allowing metal fabricators to:
- Iterate Quickly: Design changes can be implemented swiftly, leading to faster feedback cycles.
- Improve Communication: Physical prototypes can facilitate better discussions among design teams and clients.
- Enhance Testing: Prototypes can be subjected to real-world testing scenarios to validate design decisions.
Innovations in Metal Fabrication through 3D Printing
The integration of 3D printing into metal fabrication brings forth a revolutionary shift in how companies approach manufacturing. Here are some key innovations driven by this technology:
1. Customization and Personalization
Another significant advantage of prototype 3D printing in metal fabrication is the ability to create custom parts. This customization caters to unique client specifications, enhancing overall customer satisfaction. Fabricators can produce bespoke components tailored to individual needs, whether in aerospace, automotive, or medical sectors.
2. Lightweight Structures
3D printing allows engineers to design lightweight structures without compromising strength. This is crucial in industries such as aerospace, where reducing weight can lead to improved fuel efficiency and performance. Additive manufacturing facilitates the creation of intricate lattice structures, which were once unthinkable using traditional methods.
3. Complex Geometries
Traditional manufacturing processes often struggle with intricate designs due to tooling limitations. With prototype 3D printing, metal fabricators can produce complex geometries that were previously unachievable, leading to innovative products and solutions across various industries.
Case Studies: Successful Applications of 3D Printing in Metal Fabrication
Various companies worldwide leverage prototype 3D printing to revolutionize their production processes. Here are a few notable examples:
Case Study 1: Aerospace Industry
In the aerospace sector, companies like Boeing and Airbus are utilizing 3D printing for manufacturing critical components. These parts, often subjected to extreme conditions, benefit from 3D printing's ability to produce lightweight yet robust components, significantly reducing aircraft weight and enhancing efficiency.
Case Study 2: Automotive Sector
Ford Motor Company employs 3D printing for prototyping test components in vehicle production. This approach not only accelerates time-to-market but also allows for extensive iteration during the design phase, ensuring that the final products meet stringent safety and performance requirements.
Case Study 3: Medical Applications
In the medical field, 3D printing is making waves in creating customized implants and prosthetics. Companies like Materialise are developing orthopedic devices tailored to individual patient anatomy, enhancing surgical outcomes and patient comfort.
The Future of Prototype 3D Printing in Metal Fabrication
As technology advances, the potential for prototype 3D printing in metal fabrication continues to expand. Emerging trends include:
- Material Innovation: New materials are being developed, such as advanced alloys and composites, expanding the capabilities of 3D printing.
- Automation and AI Integration: The rise of automated 3D printing solutions and AI-driven design tools will further streamline production processes.
- Sustainability Practices: As industries focus on reducing their carbon footprint, 3D printing offers a path towards more sustainable manufacturing by minimizing waste and energy consumption.
Conclusion: Embracing the 3D Printing Revolution
Prototype 3D printing is more than just a trend; it is a transformative movement that is reshaping metal fabrication and manufacturing as a whole. By adopting this innovative technology, businesses can enhance their prototyping processes, improve product quality, and achieve greater efficiency. As we move forward, the companies that leverage 3D printing are likely to lead the way in manufacturing innovation, driving the future of their industries.
For metal fabricators looking to stay competitive, embracing 3D printing technology is no longer optional—it's essential. Investing in 3D printing capabilities will open doors to new opportunities and create a pathway for sustainable growth in the ever-evolving market landscape.